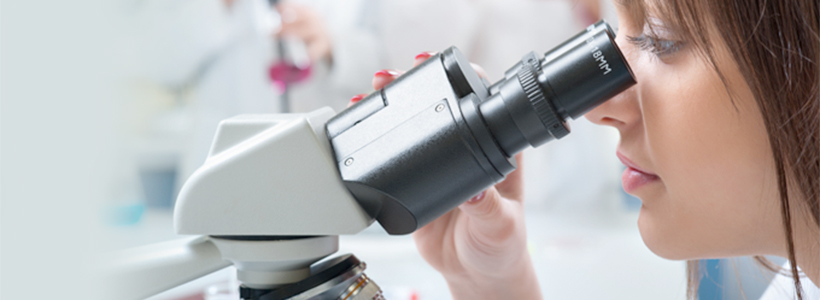
The purpose of this research paper is to examine how efficient improvement in productivity can be achieved in a selected industry by deploying Lean Manufacturing Principles & Tools. Current shop floor scenarios of the Main assembly process were discussed and improvement areas were identified were lean techniques were used to reduce the production lead time. The study used most efficient Lean methodologies such as Root cause analysis, Kaizen, MUDA & TAKT time for eliminating wastes, controlling quality and improving overall performance of the more time consuming operations of the various Main assembly processes. Time study also performed to identify the more time consuming sub processes of each of the Main assembly processes. QC tools such as Pareto chart and Cause & effect diagram were used for analysing collected data. The main aspect is to reduce the production lead time through lean techniques. After application of Lean techniques in more time consuming areas of the Main assembly process in the selected industry, there was reduction in lead time of about 20% i.e. 5 to 4 days/unit and reduction in Man hour rate of 14.3% from 112 Man Hours to 96 Man Hours Overall the production capacity was increased to 16.7% (1.2 to 1.4 Units/day) by adopting Lean methodology.